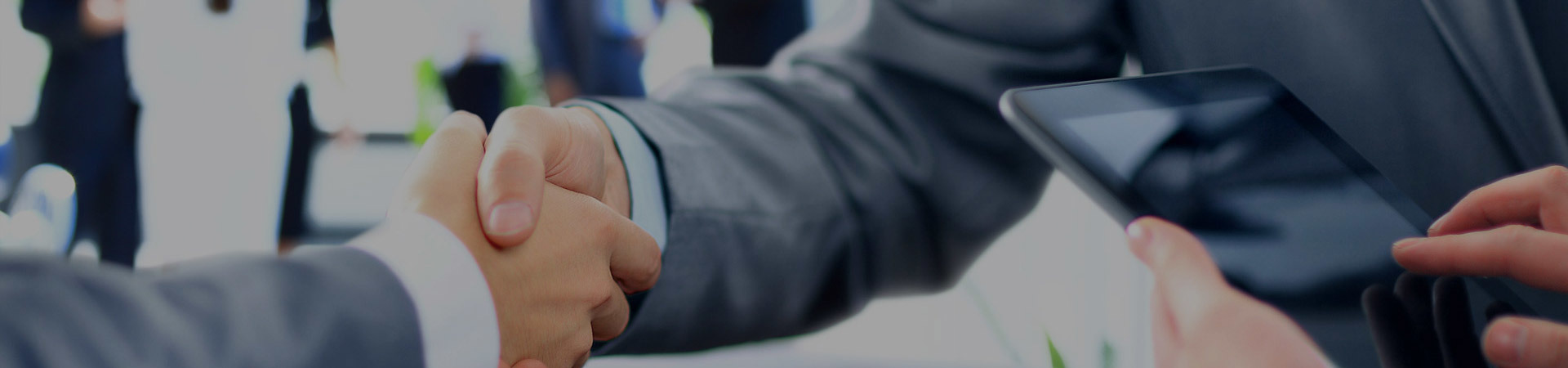
Solution
Laser welding of car door rings
1. Door Ring Structure and Material Characteristics
- Function: As a key structural component of the car body, the door ring connects the roof, sidewalls, and sill, enhancing overall rigidity and collision safety.
- Material: Usually uses high-strength steel (such as DP steel, boron steel) or aluminum alloy (such as the 6000 series), needing to balance lightweight and strength.
2. Laser Welding Technology Principle
- Process characteristics: Using high-energy lasers to melt the base material while feeding in filler wire, suitable for gap compensation and performance optimization.
- Core parameters: Laser power (1.5-6 kW), welding speed (2-10 m/min), wire feed speed (needs to match the welding speed), defocusing amount (affects penetration depth).
3. Technological Advantages
- Quality improvement: Continuous welds reduce stress concentration and improve fatigue strength.
- Lightweight: Replacing traditional spot welding, reducing the width of the lap joint, and reducing the weight of the car body.
- Efficiency and aesthetics: High-speed welding (3-5 times faster than traditional arc welding), the weld is smooth and requires no polishing.
4. Key Process Challenges and Solutions
- Parameter optimization: Determining the optimal parameter combination through orthogonal experiments or response surface methodology to avoid pores and cracks (such as adjusting the protective gas flow rate to 15-20 L/min).
- Material matching: Selecting filler wire compatible with the base material (such as ER70S-6 for high-strength steel, 4043 for aluminum alloy).
- Complex path control: Using a five-axis robot system, integrating real-time path correction, to ensure the accuracy of three-dimensional curve welding.
5. Quality Control and Inspection
- Online monitoring: Using high-speed cameras or infrared temperature measurement to monitor the molten pool dynamics in real time.
- Non-destructive testing: Combining ultrasonic testing (detecting internal defects) and X-rays (pore identification), with a sampling rate ≥5%.
- Mechanical testing: Tensile test (tensile strength ≥90% of the base material), microhardness analysis (HAZ hardness control).
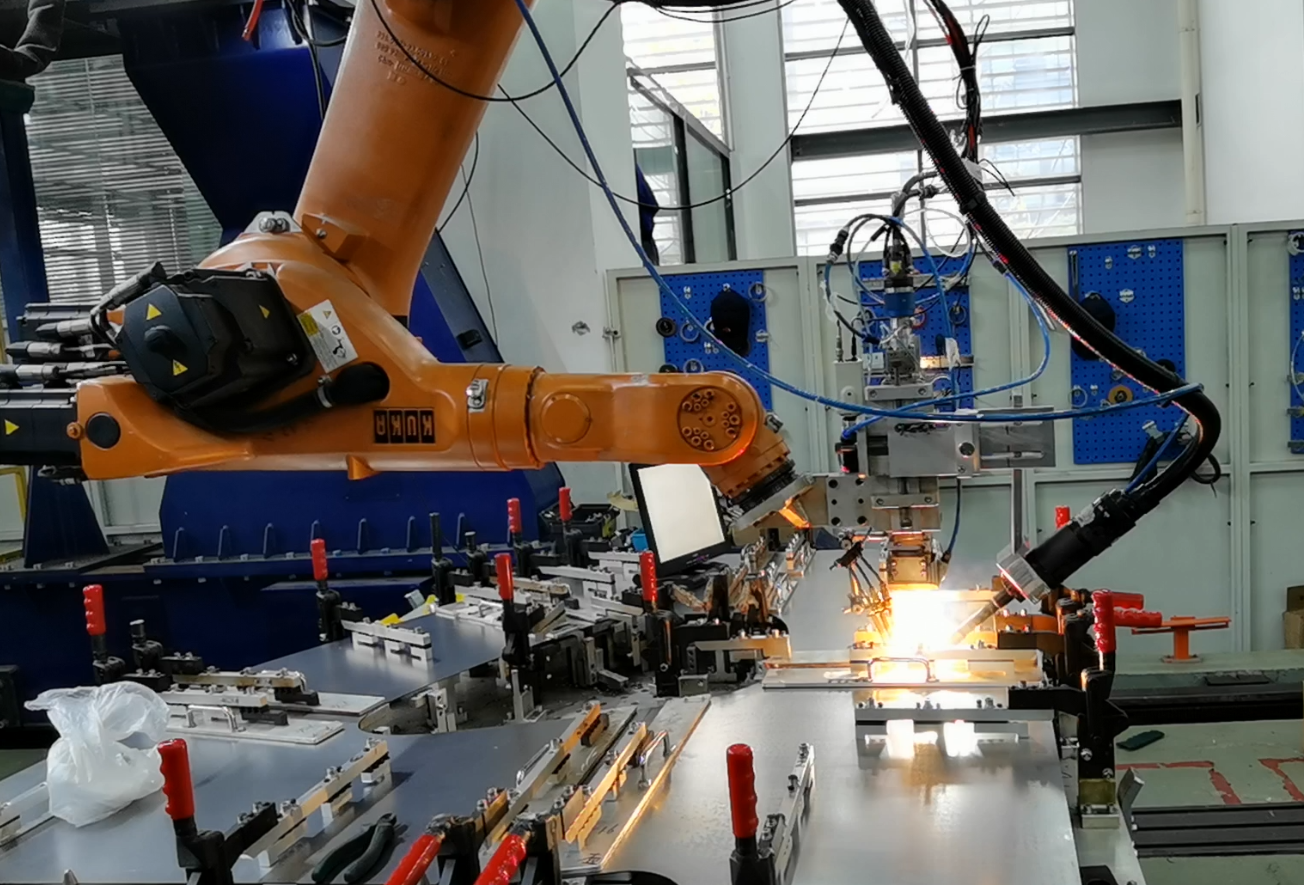