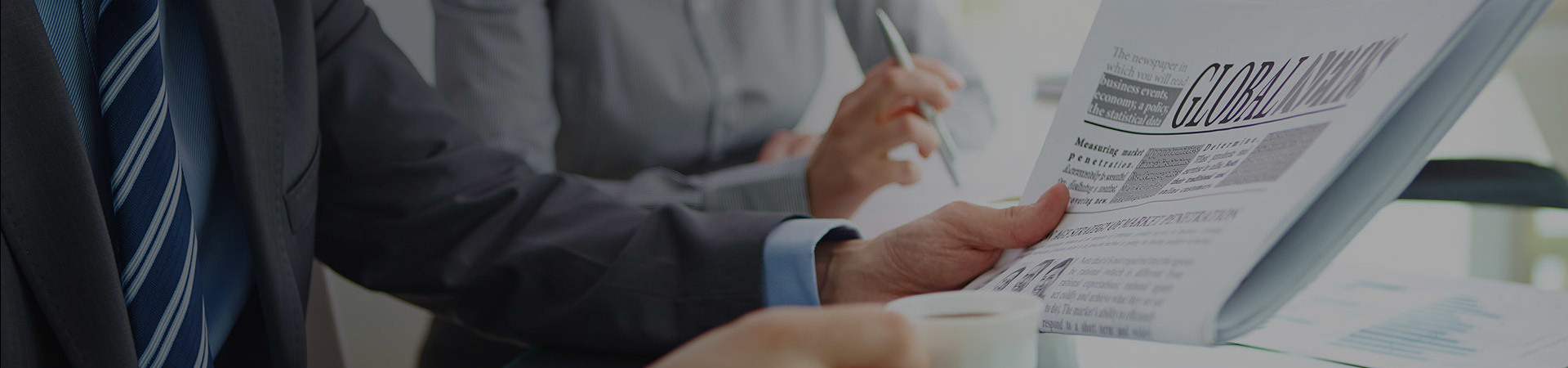
News
Applications of Laser in the Hydrogen Energy Industry
Hydrogen Production Stage
- Electrolyzer Frame and Plate WeldingIn alkaline electrolyzer production, lasers can be used for welding the frame and plates of the electrolyzer. For example, the dual-sided intelligent control welding robot for alkaline plates developed by xx laser, based on AI deep algorithms for real-time seam tracking technology, can achieve adaptive seam following and focus tracking and compensation, effectively ensuring welding quality and improving production efficiency.
- Plate CleaningLaser cleaning technology can remove impurities such as oil and oxides from the surface of the plates, improving the surface quality and performance of the plates, ensuring the efficient progress of the electrolysis reaction. Compared to traditional cleaning methods, laser cleaning has advantages such as non-contact, pollution-free, and high precision.
- Cutting of Membranes, Electrode Mesh, etc.For components such as membranes (PPS fabric), electrode mesh/screen, frame flow channels, and frame gaskets, laser cutting can achieve high precision and high efficiency. Laser cutting can precisely control cutting dimensions and shapes, reduce material waste, and improve production efficiency and product quality.
Hydrogen Storage Stage
- Hydrogen Cylinder ManufacturingIn the production process of hydrogen cylinders, laser winding technology can be used to wind composite materials to form high-strength, lightweight hydrogen cylinders. The hydrogen cylinder laser winding online monitoring system released by Jinyun Laser can achieve real-time monitoring of the winding quality of hydrogen cylinders through laser winding technology, ensuring the structural integrity of the hydrogen cylinders and improving the safety and reliability of hydrogen storage.
- Hydrogen Liquefaction Equipment ManufacturingLaser welding, cutting, and other technologies can be applied in the manufacturing of hydrogen liquefaction equipment, such as high-precision processing and assembly of components like pipes and containers in the equipment, improving the performance and reliability of hydrogen liquefaction equipment, which helps achieve efficient liquefaction and storage of hydrogen.
Fuel Cell Manufacturing Stage
- Bipolar Plate WeldingBipolar plates are one of the core components of fuel cells. Laser welding technology can tightly weld two ultra-thin metal plates with a thickness between 50μm-100μm, meeting the extremely high requirements for sealing, firmness, and flatness. Laser welding has advantages such as fast welding speed, high seam quality, and small heat-affected zone, which can improve the performance and reliability of fuel cells.
- Bipolar Plate Surface CleaningLaser cleaning can remove contaminants and oxide layers from the surface of bipolar plates, improving the surface activity and conductivity of the bipolar plates, which helps optimize the performance of fuel cells.
- Processing Related to Membrane Electrode AssembliesLaser-assisted drying technology can be used to dry the wet coated electrode layers of membrane electrode assemblies (MEA) in polymer electrolyte membrane (PEM) fuel cells, reducing the drying time from several minutes to several seconds, significantly increasing production speed, reducing energy demand, and making the production line more compact and flexible.
- Product MarkingUsing laser marking technology, permanent markings can be made on various components of fuel cells, such as marking the model, batch, production date, and other information, facilitating product traceability and quality control.